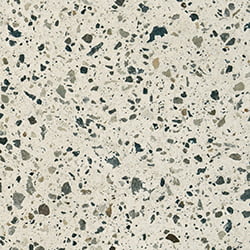
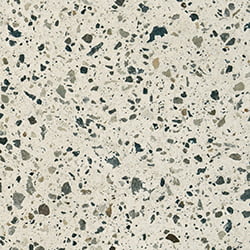
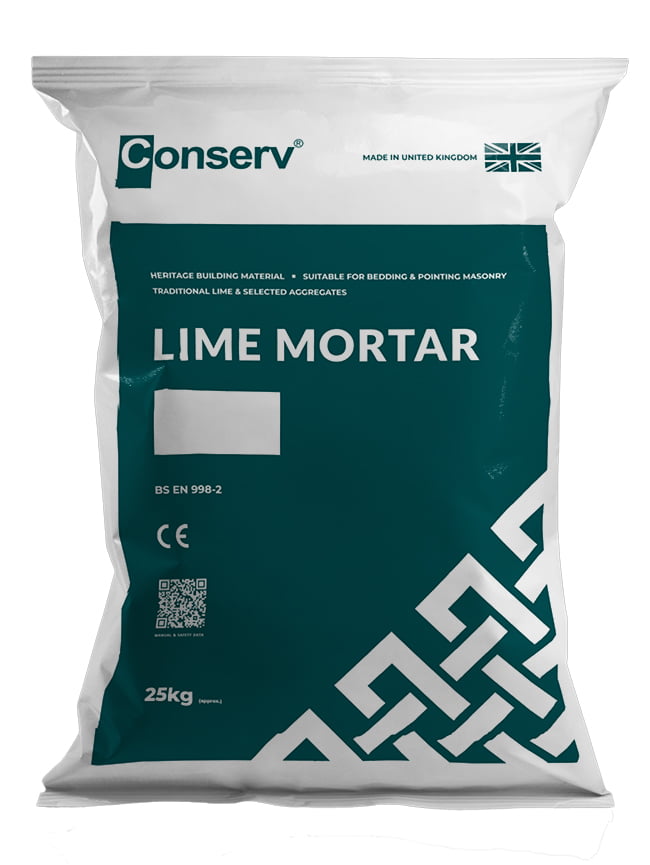
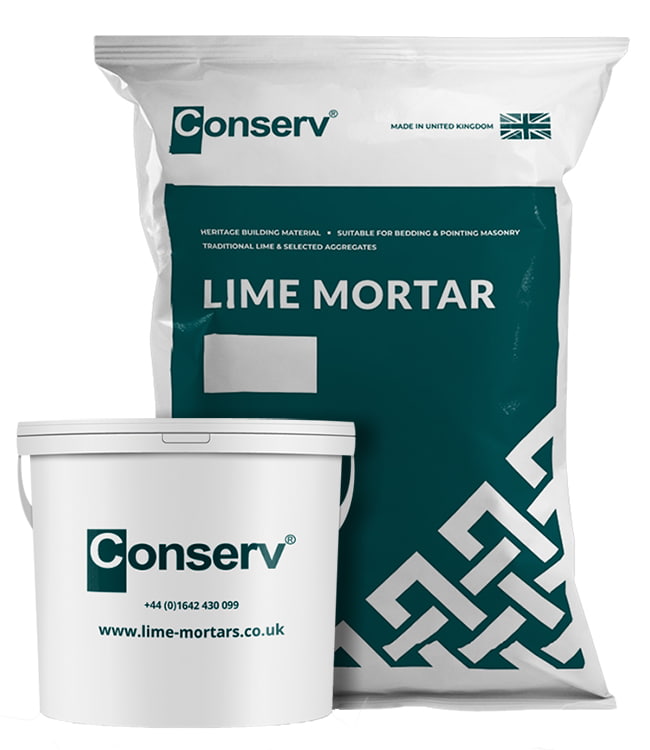
We make every effort to provide an accurate representation but images and colours may vary from the product.
Lime Mortar (Non-Hydraulic) - Coarse Stuff (25kg)
Premixed, Made with Matured Lime Putty
Traditional Lime Mortar with Matured Lincolnshire Lime
- Premixed Lime Mortar
- Made with Matured Lime Putty
- 100% Natural and Breathable
- Quality and Consistency
- Waterproof Bag (Recyclable)
- CE Certified
Best suited for soft masonry * Masonry Density Chart
Non-hydraulic lime mortar is most suited to soft / low density building materials or masonry in poor condition that is prone to decay, crumble, scale or flake and where conservation is the principal requirement.
Not suitable for use with a pointing gun
The consistency of this product is not suitable for a pointing gun. Although additional water may eventually facilitate an adequete flow, this practice should be avoided as excess water will cause the separation of lime from aggregate and thus compromise the mortar. Where a pointing gun is required see Gunlime®.
Product Details
High Standards
Non-hydraulic lime mortar is CE certified and is manufactured to British Standards BS EN 998-2:2016 following heritage guidelines.
Authentic, Pure and Simple
100% natural, breathable and sustainable. The mortar doesn't contain anything artificial, no additives or plasticisers and absolutely, certainly no cement.
Premixed
Inside the bag you'll find a premixed lime mortar, ready to use, it is made with matured non-hydraulic lime (commonly known as “lime putty” or “fat lime putty”).
Non-hydraulic lime mortars set by carbonation, very gradually. This characteristic gives the product a long shelf life providing that the material is kept sealed air-tight preventing carbonation.
The mortar may stiffen over time in storage but can be “knocked up” again and again to the ideal consistency providing it is stored correctly.
Economy & Convenience
These bags are popular with building contractors as they're economical and practical for projects large and small.
Orders for 8 or more bags are typically delivered using the UK's largest pallet network companies to keep delivery costs to a minimum.
If space is tight on-site you can call us to arrange partial delivery of your goods on different dates. We'll find a solution that works best for you.
Technical †
- Specification
- BS EN 998-2:2016
- Binder
- Lime Putty BS EN 459-1:2015
- Density
- 1,525 kg/m³ ± (at 91 days)
- Vapour permeability
- 0.92 grams / 100mm² / 24hrs ±
- Compressive strength
- 0.75 N/mm² ± (at 91 days)
- Flexural strength
- 0.74 N/mm² ± (at 91 days)
- Resistance to freeze thaw
- Low (10 cycles)
- Resistance to sulphate exposure
- High (26-50 cycles)
- Resistance to freeze thaw in sulphate conditions
- Low (10 cycles)
- Capillary Rise
- Very High (126-150mm in 6 hours)
- Mortar durability class
- 1 to 2
- Carbonation Rate
- High
- Initial Set
- Overnight ±
- Curing
- 2mm per calendar month ±
- Shelf Life §
- Long shelf life, potentially in excess of 12 months if sealed airtight for storage
- Colour
- Neutral
- Tone ‡
- Light
- Texture
- Coarse
- Grading
- Gc85/20
- Bed size
- 12mm ≥
* Masonry density can vary by quarry, manufacturer, age and condition of material, this information serves only as a general guide, disclaimer.
† Technical data is approximated as it can vary significantly depending on various factors, particularly weather conditions. The information presented outlines typical behaviour you might expect in the United Kingdom with ambient temperatures of 10°C in sheltered areas with low exposure to wind and moisture. The information is nevertheless useful to establish the relative properties and performance of different products, disclaimer.
§ Product must be sealed airtight in their packaging during. Material will stiffen over time when sealed but can be N'knocked up' back to a workable state.
‡ The colour of the mortar will continue to lighten until it fully cures. This difference in colour can be quite dramatic. In good weather, the mortar will appear much lighter after 10 days.
Disclaimer It is the customer's responsibility to determine the suitability of this product. Samples should be prepared and approved before complete application of this product. Appropriate testing should be undertaken prior to application where compressive strength or density are a critical factor.